Hydrolox Engine: Difference between revisions
No edit summary |
No edit summary |
||
Line 5: | Line 5: | ||
For rockets that want to be as lightweight as possible, this is the propellant mix to use. But they won’t be the smallest possible as hydrogen is extremely un-dense and deeply cryogenic. This makes designing a propellant tank for it difficult enough, if the hydrogen didn’t also try to leak out from between the atoms of the tank walls. | For rockets that want to be as lightweight as possible, this is the propellant mix to use. But they won’t be the smallest possible as hydrogen is extremely un-dense and deeply cryogenic. This makes designing a propellant tank for it difficult enough, if the hydrogen didn’t also try to leak out from between the atoms of the tank walls. | ||
{| class="wikitable | ==Introduction== | ||
Since the early 1960s, hydrogen and oxygen rockets have been the propulsion system with the highest exhaust velocity to anyone designing a launch vehicle. Trying to get high exhaust velocity meant sacrificing all useful thrust, as with an electric thruster, using much scarier chemicals, like fluorine, or developing a very different propulsion system such as nuclear rockets. | |||
Hydrogen-oxygen or ‘hydrolox’ has created the highest performance stages we have ever launched, such as Saturn V’s S-IVB third stage or the Centaur V upper stage. | |||
From a simplistic standpoint, there is no reason to use anything but hydrolox mixes. The real world is not so simple. Other factors come into play that reduce the attractiveness of hydrolox engines. They can be critical obstacles, like the huge volume of propellant tanks meant to contain liquid hydrogen with a density of just 70 kg/m^3 when liquid at near boiling point creating too much drag for spaceplanes to accelerate, to minor things like liquid hydrogen being more expensive than kerosene. | |||
Many missions won’t even make use of hydrolox engines’ superior exhaust velocity. Low deltaV requirements means that performance is wasted. Long duration missions are also less suited to hydrolox propulsion, as storing liquid hydrogen against the heat of unfiltered sunlight beating down on gigantic propellant tanks is a real pain. | |||
===Engine Performance=== | |||
This is an example based on RS-25D engine running at its maximal 109% throttle rating. | |||
{| class="wikitable" | |||
|+Engine Performance | |+Engine Performance | ||
|- | |- | ||
Line 38: | Line 49: | ||
|1590 kW/kg | |1590 kW/kg | ||
|} | |} | ||
==Design and Function== | ==Design and Function== |
Revision as of 18:08, 22 September 2021
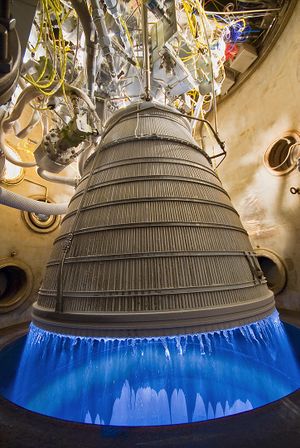
Of all the fuel and oxidizer combinations that do not actively try to eat their way out of propellant tanks, hydrogen and oxygen have the highest performance. The chemical reaction of the two propellants produces a very hot flame and the exhaust, water, exits at a higher velocity than practically anything else. In fact, it burns so hot that most engines move away from the ideal ratio of hydrogen to oxygen to reduce the temperatures inside their combustion chambers.
For rockets that want to be as lightweight as possible, this is the propellant mix to use. But they won’t be the smallest possible as hydrogen is extremely un-dense and deeply cryogenic. This makes designing a propellant tank for it difficult enough, if the hydrogen didn’t also try to leak out from between the atoms of the tank walls.
Introduction
Since the early 1960s, hydrogen and oxygen rockets have been the propulsion system with the highest exhaust velocity to anyone designing a launch vehicle. Trying to get high exhaust velocity meant sacrificing all useful thrust, as with an electric thruster, using much scarier chemicals, like fluorine, or developing a very different propulsion system such as nuclear rockets.
Hydrogen-oxygen or ‘hydrolox’ has created the highest performance stages we have ever launched, such as Saturn V’s S-IVB third stage or the Centaur V upper stage.
From a simplistic standpoint, there is no reason to use anything but hydrolox mixes. The real world is not so simple. Other factors come into play that reduce the attractiveness of hydrolox engines. They can be critical obstacles, like the huge volume of propellant tanks meant to contain liquid hydrogen with a density of just 70 kg/m^3 when liquid at near boiling point creating too much drag for spaceplanes to accelerate, to minor things like liquid hydrogen being more expensive than kerosene.
Many missions won’t even make use of hydrolox engines’ superior exhaust velocity. Low deltaV requirements means that performance is wasted. Long duration missions are also less suited to hydrolox propulsion, as storing liquid hydrogen against the heat of unfiltered sunlight beating down on gigantic propellant tanks is a real pain.
Engine Performance
This is an example based on RS-25D engine running at its maximal 109% throttle rating.
Name | RS-25D |
ISP or Exhaust Velocity | 366s <-> 3590 m/s (sea level) 452s <-> 4434 m/s (vacuum) |
Thrust | 1,860,000 N (sea level) 2,279,000 N (vacuum) |
Efficiency | 71% |
Drive Power | 5052 MW |
T/W | 73.1 (vacuum) |
Energy Source (Fuel) | Hydrogen + Oxygen at 6:1 ratio |
Propellant | Water exhaust |
Reactor | Combustion chamber |
Power Density | 1590 kW/kg |
Design and Function
Hydrogen-oxygen engines are, like most chemical engines, fairly simple. You get some hydrogen, you get some oxygen, you pump them into a chamber, you introduce a spark or other ignition source, and steam comes out the back glowing with a very pretty clear flame, sometimes with varying minor coloration.
Hydrolox engines are almost universally fuel-rich and make great use of the excess hydrogen by using it as a coolant for regenerative cooling. This is when propellant flow is used to extract heat from the hottest parts of the engine, such as the nozzle throat, and then adding it into the reaction chamber to improve overall efficiency.
The biggest source of design variations is in how the propellant pumps are powered.
The J-2 used a gas generator, having a secondary burner to power the turbopumps. The J-2S cut that, by tapping off a portion of the main chamber gas flow, and avoiding a separate combustion chamber. You can get more complex, like the multi-stage booster pumps the SSME used to get to nearly 207 bars of pressure. Alternately, you can go dead simple--the expander cycle cleverly manages to harvest all the pumping energy it needs for low-pressure vacuum engine operation from the hydrogen used to cool the chamber and nozzle bell, meaning the turbine inlet gas is only mildly warm. That’s perfect if you want to use turbopump blades made out of a lightweight and strong material that can’t handle high temperature gases, like aluminium alloys.
Performance / Capabilities / Applications
The main benefit of hydrolox is its performance: even a moderate pressure engine with a vacuum nozzle can break 440 seconds of specific impulse. No other engine type in present-day service can reach those levels of performance. At the same time, hydrogen is a fantastic coolant, more than an order of magnitude better than any other fuel, meaning it’s possible to build some incredibly clever engine cycles without problems like turbine temperature or propellant “coking” of hydrocarbons.
As an example of the cleverness this allows, the turbine inlet temperature on the expander cycle RL-10 is below the boiling point of water, more like a kitchen appliance than the complex high-temperature turbomachinery needed in other fuels.
Similar endurance and robustness was seen with the J-2 engines for Saturn. The [i]Space Shuttle Decision[/i] by T A Heppenheirner quotes Rocketdyne's Paul Castenholz, one of the engineers managing J-2 development. "We never wore out an engine of the J-2 type. We could run it repeatedly; there was no erosion of the chamber, no damage to the turbine blades. If you looked at a J-2 after a hot firing, you would not see any difference from before that firing. The injectors always looked new; there was no erosion or corrosion on the injectors.” As Heppenheimer reports, this was inspired by examples like a single test engine which ran for 103 starts and 6.5 hours without overhaul. Higher performance hydrolox engines like the Space Shuttle Main Engine (SSME) have a more complex reputation, though more recent tests of the AR-22 variant demonstrated 10 firings in 10 days with no major overhaul. With good performance from even relatively simple engines, it’s no wonder that rocket pioneers like Werner Von Braun were swayed to the Cult of Hydrolox from initial skepticism. For more than half a century, it’s been the propellant of choice for upper and sustainer stages for most American launch vehicles from Atlas to Delta to the Space Shuttle. For that reason, if you want performance with near-term engines, hydrolox has a lot to recommend it.
The downside of hydrolox is the blasted hydrogen. Its performance comes from hydrogen’s low molecular mass--about the smallest anything can get and be legitimately called a molecule--but that also means it has to be incredibly cold to be liquid, at about 20 C colder than liquid oxygen. That’s troublesome for long duration storage, making “boiloff” the word of the day. Heat will get to your hydrogen any way it can, and before long, you won’t have any left. Even once kept liquid, the density is incredibly poor. That means heavier and physically larger tanks for the same performance. Even with hydrogen’s improved specific impulse, the Hydrolox Delta IV lower stage had to be five meters in diameter to lift the same payloads as the 3.8m Atlas V, since hydrolox has about a third the mixed density of kerolox.
Worked Example(s)
Planned to go here:
- RL-10 expander
- J-2S gas-gen
- SSME
- Maybe M-1 massive gas gen?
Additional References
GRAB SHUTTLE DECISION LINKS